The most common electropump problems and how to deal with them.
It can happen, even if it is a quality product, that an electric pump has problems, for example that it does not pressurise or that it overheats.
These situations, like many others, are part of the life of an hydraulic electric pump and it is therefore essential not only to identify the most common problems, but also to know how to deal with them and implement the right measures, both in terms of solutions and maintenance. Let us not forget, in fact, that maintenance plays a crucial role both because it helps prevent problems and because it allows the electric pump to function optimally, thus saving energy and increasing its lifespan.The pump overheats: the danger of dry running.
When an electric pump runs without liquid inside it, it is said to 'run dry'. This situation is highly detrimental to the electric pump, as it causes friction of the internal parts and general overheating. The consequences are many and all quite important: from the motor burning out, to the mechanical seals breaking down, to the impeller melting and the shaft failing.Various devices, often incorporated in the electric pumps themselves, are used to prevent the damage caused by dry running.
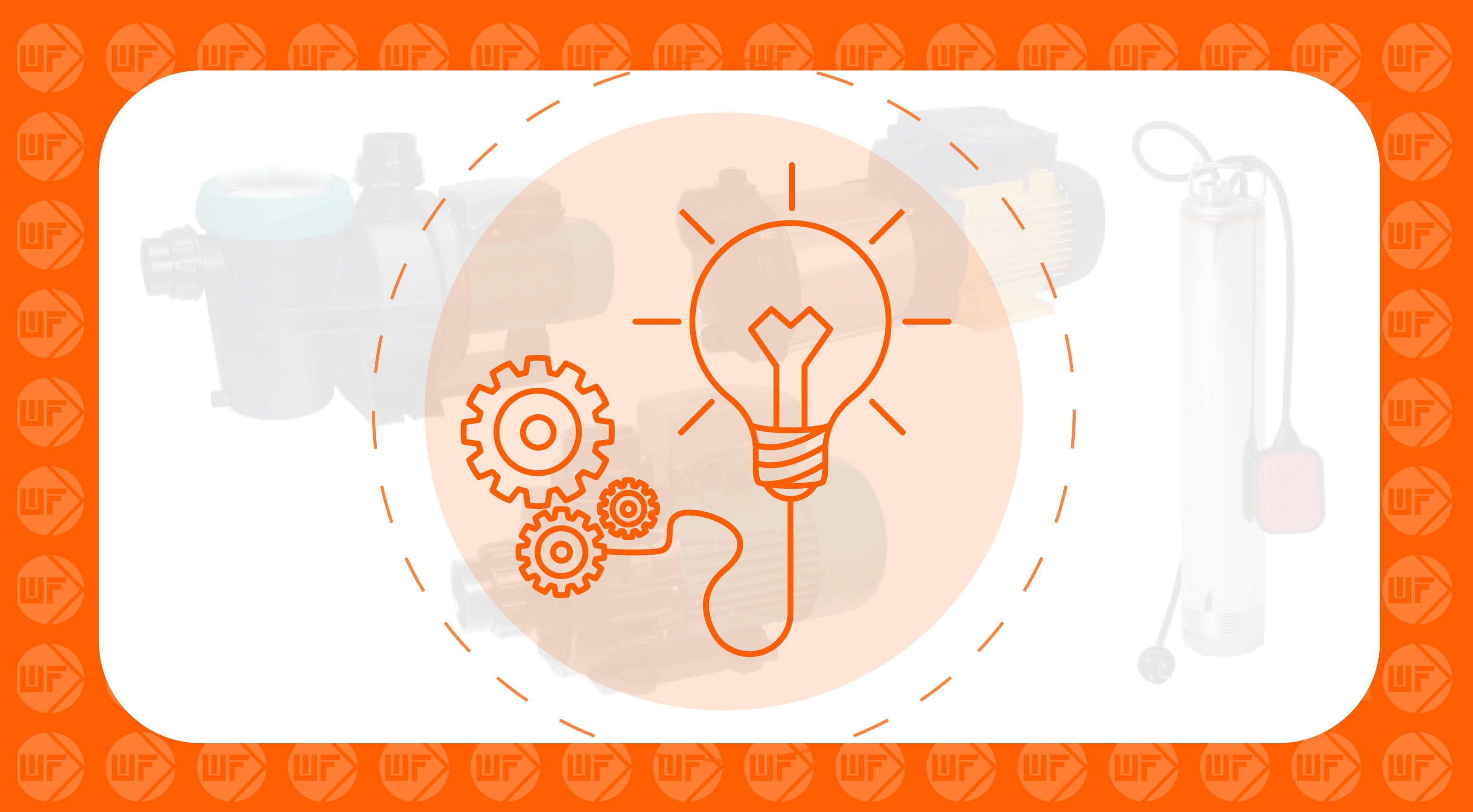
This is the case with level probes and pressure switches that guarantee an automatic stop in the event of a lack of fluid. In addition, it is a good rule to install a check or non return valve in the suction. This prevents the system from running dry when the pumping system stops. Therefore, when the system restarts, the danger of dry running is avoided.
Still on the subject of mechanical seals, in addition to operation with no or little fluid, wear can be caused by inadequate lubrication or incompatibility with the fluid handled. Hence the importance of choosing the most suitable mechanical seal and carrying out proper maintenance.
Suction problems: when the pump doesn't pull water.
What might appear to be a serious problem, linked to a pump failure, actually depends in most cases on simpler causes.
First of all, the suction depth must be checked; it must not be greater than the pump's capacity. Another aspect to consider is the suction pipe, to rule out obstruction, constriction or kinking.It is also important that there are no air bubbles inside, which can occur in the case of holes or connections that are not perfectly tight.
Pump noise and vibration: signs not to be underestimated.
The production of abnormal noises should warn of the operation and health of the bearings. These are components that are easily subject to wear and this has major consequences for the entire mechanism. Very often the bearings are damaged by incorrect belt tensioning, which can lead to motor failure. A proper bearing maintenance plan and careful lubrication can help prevent overload and wear. Electric Pump vibrations should also always be carefully considered. The presence of slight vibrations is normal, but if these become excessive, it may be the result of poor balancing of the rotating parts that needs to be investigated. Let us not forget, in fact, that the consequence of vibrations is not only possible mechanical failures but also higher consumption.
Cavitation: one of the main problems with electric pumps.
This problem arises from a very common physical phenomenon in hydraulic machines. In a nutshell, it is the formation of steam bubbles whose instantaneous collapse generates micro-jets at very high pressure, which in the long term cause damage to the pump.
What occurs, in particular, concerns:
- a deterioration in the performance of the pump, which can be estimated as a decrease in efficiency of at least 3%;
- the excessive vibration and damage of the pump's internal components. Microjets erode the solid surface of metals, forming what are called 'erosive pits'.
How to prevent and solve the problem of cavitation?
First of all, it is important to consider that the high pressure drop in the suction line and the high difference in level between the electric pump and the suction tank can favour the occurrence of the phenomenon. One suggestion would be to increase the diameter of the pipework and decrease the length of the suction path, use a submersible pump if necessary, and use pumps with a NPSH (Net Positive Suction Head, i.e. total suction height net of vapour pressure) as low as possible.