What can we do when your level switch does not work really properly?
When a float level switch stops functioning properly, it is essential to carry out some preliminary checks before proceeding with a return request.
The steps below are crucial to identify the reason for a potential problem with the hydraulic floating switch and to determine whether the device can be repaired or if it actually needs to be returned and therefore replaced.
Visual check of the floating level switch.
Checking the external condition: the hydraulic float body and its cable.
The first control point is a visual inspection of the level switch and its cable. It is in fact advisable to check the integrity of the float body and ensure that there is no visible damage, such as cracks or openings that could have compromised its integrity and impermeability. It is also a good idea to check the level switch cable for any signs of manipulation, such as cuts or splices, that could have compromised its functionality. In any case, changes made to the cable or visible damage to the hydraulic float may invalidate the return and replacement of the product.
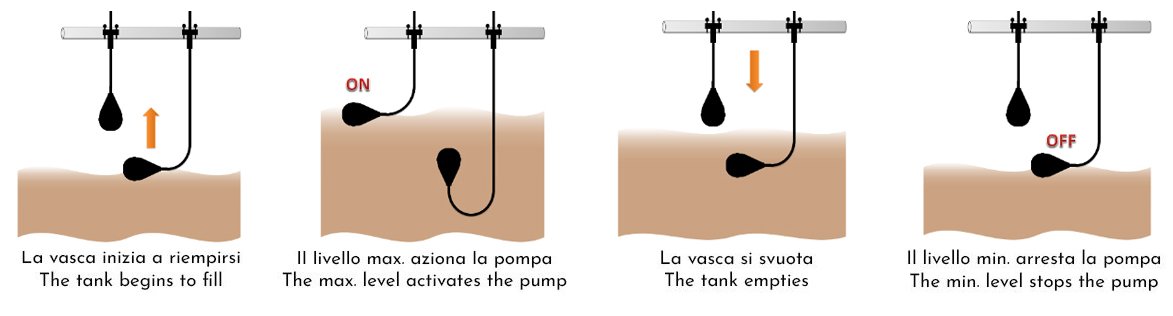
Production date and proof of purchase of the floating switch.
It is essential to check the production date of the hydraulic floating switch, which is usually indicated by an imprinted mark or label with the date of manufacture and sealing. This detail is essential to verify that the level switch falls within the 24-month warranty period required by European legislation (produt made in EU). Without valid proof of purchase, the floating switch may be considered out of warranty and therefore not replaceable.
Electrical test of the level regulator.
A multimeter, multitester or simple tester set to continuity mode is used to check the integrity of the float switch's internal circuit. This test also helps identify possible malfunctions at the microswitch.Testing the level switch in a pressure and vacuum tank.
These tests are normally carried out by the hydraulic float manufacturer as they require dedicated equipment and personnel. Basically, conditions must be created within these tanks that simulate the conditions to which the floats may be subjected during daily use.
Pressure tank test of the level switch
Preparation: The level regulator is placed in a special tank that can be sealed and pressurised. It is important that the float is installed and connected as in a typical working configuration to ensure that the test reflects actual operating conditions.
Pressurisation: The tank is sealed and the internal pressure is gradually increased by means of a hydraulic pump. The pressure increase simulates overload conditions that the hydraulic float may encounter, such as in heavy industrial applications or high-pressure environments.
Monitoring: During the test, the float's response to the applied pressure is monitored. Particular attention is given to the activation and deactivation of the level switch, which should operate reliably despite pressure variations.
Evaluation: At the end of the test, the float is inspected for any damage or failure in the mechanism caused by the pressure. This may include checking for leaks, deformations or internal electrical circuit failures.
Depression tank test of the level switch.
Preparation: Similar to the pressure test, the float is placed in a tank that can be sealed. In this case, the device must be configured to reflect a typical installation.
Depressurisation: The tank is sealed and the air inside is evacuated to create a vacuum. This simulates vacuum conditions or very low pressures, which could be experienced in specific level controller applications or high altitude environments.
Monitoring: During the test, it is observed how the float and its level switch respond to pressure reduction. The level regulator must maintain its functionality despite the drastic change in ambient pressure.
Evaluation: At the end of the test, the float is examined to ensure that there has been no structural or mechanical damage caused by the depression, such as collapse of the float body or malfunction of the trigger mechanism.
Dissection.
This test, which involves the destruction of the level regulator, is normally carried out by the manufacturer's technical department or specialised companies and requires great care as the dissection of the level switch must not compromise the internal parts and render the test useless. The sectioning must be carried out in different ways depending on the type of float.