Pressure switches and pressure flow switches for monitoring pressure in hydraulic systems.
Hydraulic pressure switches are key components in hydraulic systems and play a critical role in ensuring the safety, efficiency and functionality of various hydraulic applications.
Over the years, these devices have evolved, becoming indispensable in numerous sectors and applications. This article takes an in-depth look at hydraulic pressure switches, exploring their history, different types and main applications. In addition, we will discuss the importance of the materials used in their construction and examine common products closely associated with them.Hydraulic pressure switches and pressure flow switches: a brief overview.
The origins of hydraulic pressure switches date back to the mid-20th century, coinciding with the rise of hydraulic systems in all industries. The first pressure switches were relatively simple and were mainly used for safety purposes, such as preventing overloading of the hydraulic system. Over time, advances in technology and materials led to more sophisticated and versatile pressure switch designs.Types of hydraulic pressure switches and pressure flow switches.
Today, hydraulic pressure switches are available in various types, each of which is suitable for specific applications and operating conditions.The main types include:- Diaphragm pressure switches: these pressure switches use a flexible membrane to detect pressure variations. they are commonly used in applications requiring high precision, such as industrial automation and precision machining. All pressure switches from Water Fitters are all membrane pressure switches and differ in size, capacity and associated instrumentation (e.g. Floypress RM pressure switch with manometer).
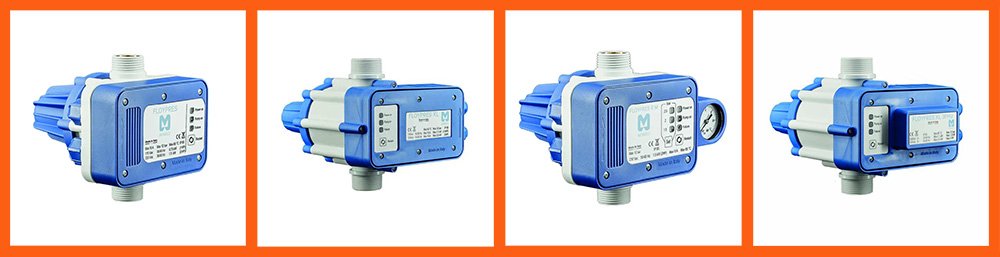
- Pistons pressure switches: use a piston or plunger to detect pressure variations. They are ideal for applications requiring fast response times, such as hydraulic brake systems in the automotive and aerospace industries.
- Bourdon tube pressure switches: use a curved tube that straightens as pressure increases. They are widely used in industrial applications, including hydraulic power packs and process control systems.
- Bellows pressure switches: these are suitable for applications with corrosive or high-temperature fluids due to their hermetic design. They are used in chemical processes and in the oil and gas industries.
Applications of hydraulic pressure switches.
The importance of hydraulic pressure switches lies in their ability to monitor and control pressure levels in hydraulic systems. They perform several critical functions, acting in terms of:- Safety: they prevent system overloads and protect equipment and operators from potential hazards
- Efficiency: they optimise system performance by keeping pressure within desired ranges, reducing energy consumption and component wear.
- Control: they allow precise control of hydraulic systems, ensuring their operation within specified parameters
- Monitoring: provide real-time feedback on pressure conditions, facilitating diagnostics and maintenance
Materials and operating principles of hydraulic pressure switches.
The choice of materials for hydraulic pressure switches is crucial for their reliability and durability. The most common materials are stainless steel, brass, polypropylene and various elastomers for the sealing components. Stainless steel or polypropylene are preferred for parts in contact with the fluid, due to their corrosion resistance and high pressure capabilities. The choice of materials depends on the fluid used and the environmental conditions in which the switch operates.
Hydraulic pressure switches operate on the principle of mechanical deformation or pressure-induced displacement. When the pressure in the hydraulic system reaches a predetermined value, a mechanical response is triggered within the pressure switch. This response can take the form of diaphragm deflection, piston movement or tube straightening, depending on the type of pressure switch. This mechanical action, in turn, activates an electrical circuit, signalling the control system to take specific actions, such as stopping a machine or adjusting system parameters.
Products associated with hydraulic pressure switches.
Hydraulic valves: often used in conjunction with hydraulic pressure switches are pressure relief valves to ensure the safety of hydraulic systems. When pressure exceeds safety limits, the pressure switch sends a signal to the hydraulic valve, which opens to release excess pressure, preventing catastrophic failure.
Hydraulic pumps and hydraulic motors: hydraulic pressure switches are essential to ensure the operation of hydraulic pumps and motors, as they monitor pressure levels to prevent damage or malfunctions to these expensive and critical hydraulic components. In this case, pressure or pressure switches can trigger shutdowns or adjustments to maintain optimal operating conditions.
Hydraulic power units and pressurisation units: used in various sectors such as manufacturing and construction, pressure switches maintain constant pressure levels in hydraulic systems, instruments and machinery. Pressure switches ensure that the hydraulic power unit operates within safe parameters, guaranteeing constant water pressure in the hydraulic system and reducing the risk of downtime and maintenance costs.
Process control systems: In industrial automation and production, hydraulic pressure switches play a key role in process control systems. They help maintain accurate pressure levels, ensuring product quality and consistency in processes such as injection moulding, metal forming and hydraulic presses.
Conclusion.
Hydraulic pressure switches they have gone a long way since their inception, evolving to meet the needs of modern hydraulic systems in various sectors. Their importance in ensuring safety, efficiency and precision is undisputed. With a wide range of types and materials, these switches are suitable for different applications and environmental conditions. In addition, their integration with complementary products such as safety hydraulic valves and pumping system improves the overall performance and reliability of hydraulic systems, thus making pressure switches indispensable in today's hydraulic, building and industrial landscape.