The winery's hydraulic system: the efficiency behind every good wine.
Wineries are often a fascinating blend of tradition and innovation.
- The hydraulic system is a fundamental component of the winery.
- The choice of stainless steel valves and fittings guarantees hygiene and durability.
- Summer is the ideal time to carry out preventive maintenance on the system.
On the one hand, there are methods handed down from generation to generation, culture and the bond with the land, and on the other, the technological aspect cannot be overlooked. The hydraulic system of a winery, in particular, is a clear example of technology serving the production of a quality product, controlled in all stages of grape processing.
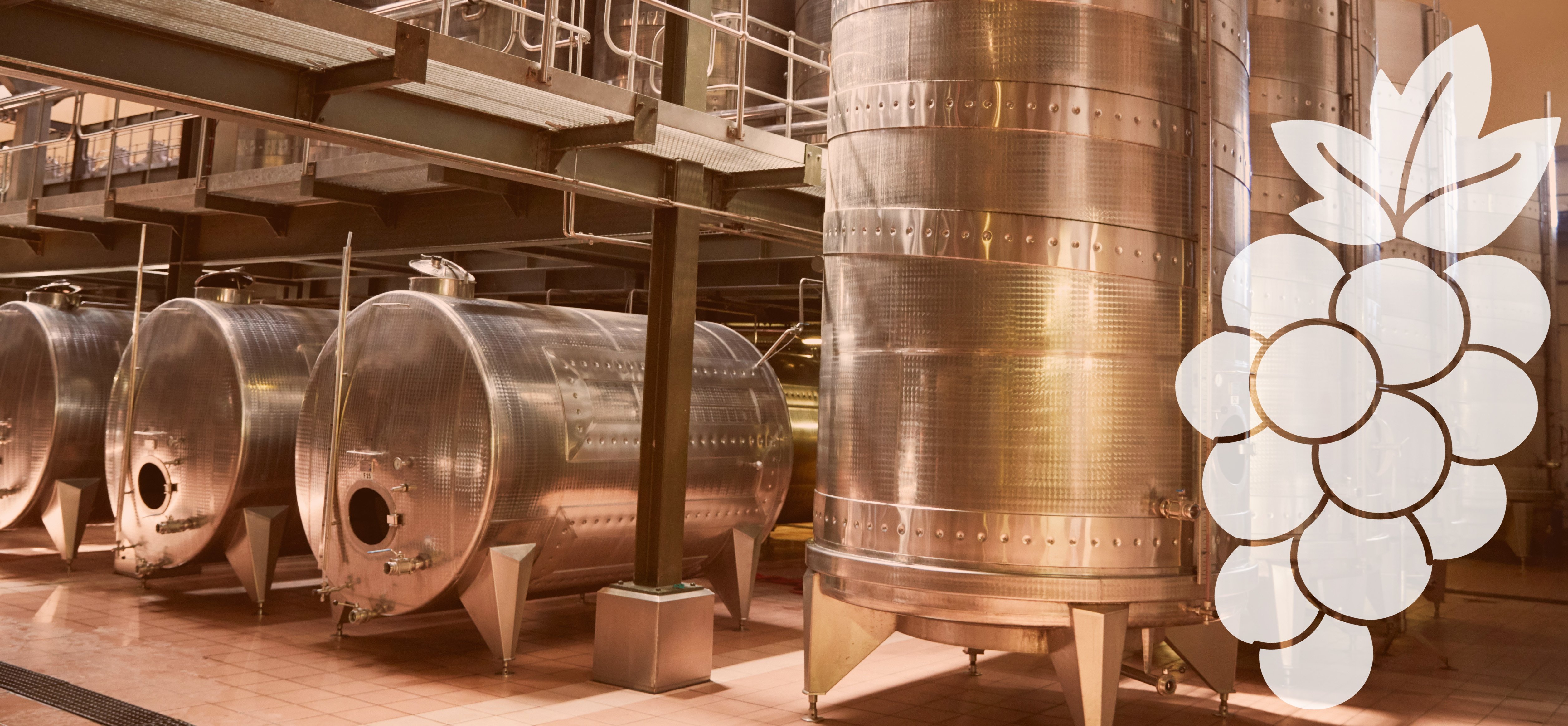
The hydraulic organization of a winery.
The design of a winery system requires the structuring of an internal hydraulic network where valves, fittings, and stainless steel components are essential elements to ensure hygiene, durability, and fluid control in winemaking processes.
The hydraulic system of the winery is used for distributing water (potable, cleaning, or technical), managing wastewater and discharge, and transferring wine and must through specific lines or circuits during the various stages of production.
Among the hydraulic components for wineries, alongside pumping systems, we first find the valves:
- Check valves, to prevent backflow during transfers or in washing lines;
- Ball valves, for controlling and intercepting the flow;
- Butterfly valves, for high-flow systems;
- Three-way valves, to divert flow in recirculation circuits.
Stainless steel valves for winemaking: why they are the industry standard.
A first consideration concerns the material of the valves. The use of AISI 304 and AISI 316 stainless steel valves in wineries is the standard choice, recommended for several technical and hygienic reasons. Stainless steel valves are resistant to chemicals and cleaning agents, ensure low maintenance and long service life. They also offer excellent hygiene: the smooth surface is easily washable and sterilizable and does not retain organic residues.
For winery automation, valves can be motorized, allowing flows to be controlled precisely, safely, and programmatically. In this way, processes are optimized, timing is faster, and safety is increased thanks to reduced manual work.
The advantages of stainless steel fittings for the wine industry.
The various hydraulic components of the winery – pipes, valves, pumps, and tanks – are connected through different types of fittings. These can be threaded, flanged, clamp, or weld. The choice always depends on use and required disassemblability. As with the valves, AISI 304 or AISI 316 stainless steel is the recommended material, unbeatable in terms of hygiene, corrosion resistance, durability, and system flexibility.
Summer: the key moment to inspect your winery’s hydraulic system.
In the world of wine, attention to detail doesn't stop at the grape because the technical infrastructure of a winery makes a difference. The organization of the hydraulic system, often invisible but essential, directly affects hygiene, food safety, production efficiency, and the quality of the final product.
Of course, only smart design allows optimized flows and minimal maintenance. Still, the latter remains important. And with summer approaching and the harvest season just around the corner, it is time to check the efficiency of the hydraulic system.
Operations must include valve and gasket inspection to avoid anomalies that could compromise operations during the production peak.
Thorough circuit cleaning is also essential, made easier by removable and easily inspectable components, as well as the use of a highly hygienic material like stainless steel.
Particular attention should be paid to filters, crucial for ensuring the quality of the water used during cleaning and processing phases. Clogged or poorly maintained filters can reduce pressure, compromise hygiene, and slow down operations.
Checking their condition, replacing them if necessary, or opting for self-cleaning or easy-to-replace cartridge models allows safe and continuous work, reducing the need for corrective interventions in peak season.