Hydraulic manifolds: streamlining efficiency and performance.
Hydraulic manifolds have revolutionized fluid control systems in a variety of industries. With a history rich in innovation, these versatile components have become an integral part of the operation of pressurization units and heating systems.
This article explores the importance of hydraulic manifolds in these applications, highlighting their role, the materials used in their construction, and the benefits they bring to the hydraulic systems into which they are integrated.
How hydraulic manifolds work.
Here is a general overview of how hydraulic manifolds work and its main components:- Structure: they generally consist of a solid block or plate, often constructed of materials such as steel or aluminum. They feature a series of machined channels, ports and cavities;
- Fluid inlet and outlet points: hydraulic manifolds have multiple ports that serve as hydraulic fluid inlet and outlet points. These ports are designed to connect to various system components, such as hydraulic pumps, shut-off valves, cylinders or tanks, and filters.
- Channels and cavities: within the hydraulic manifold structure are channels and cavities that direct the flow of hydraulic fluid. These paths are designed to route fluid between different ports and components.
- Integration of hydraulic valves: they may integrate valves directly into their structure or not. Valves can be mounted on the manifold, allowing precise control of fluid flow. Valves can be operated electrically or by other means and regulate the passage of fluid through specific channels and ports.
- Fluid distribution: the hydraulic manifold acts as a central distribution point for hydraulic fluid. It normally receives fluid from the hydraulic pump and distributes it to the different parts of the system according to the desired operation and ensuring that the fluid reaches the different components, such as actuators or control valves, in the required sequence and at the right pressure and flow rate.
- Control and regulation: by incorporating valves and other control elements, hydraulic manifolds enable precise control and regulation of fluid flow. Valves can be open, closed, or partially open to direct fluid to specific areas or control the speed and force of hydraulic actuators. The design and configuration of the hydraulic man ifold determine the specific flow paths and overall functionality of the hydraulic system.
- Pressure relief: hydraulic manifolds may also include pressure relief valves or other safety mechanisms to protect the system from excessive pressure. These valves can divert excess fluid to a reservoir to prevent damage to hydraulic system components.
In general, manifolds play a crucial role in hydraulic systems by directing and controlling fluid flow. In other words, they provide a centralized solution for the distribution of liquids and gases, enabling efficient and precise operation of various hydraulic components.
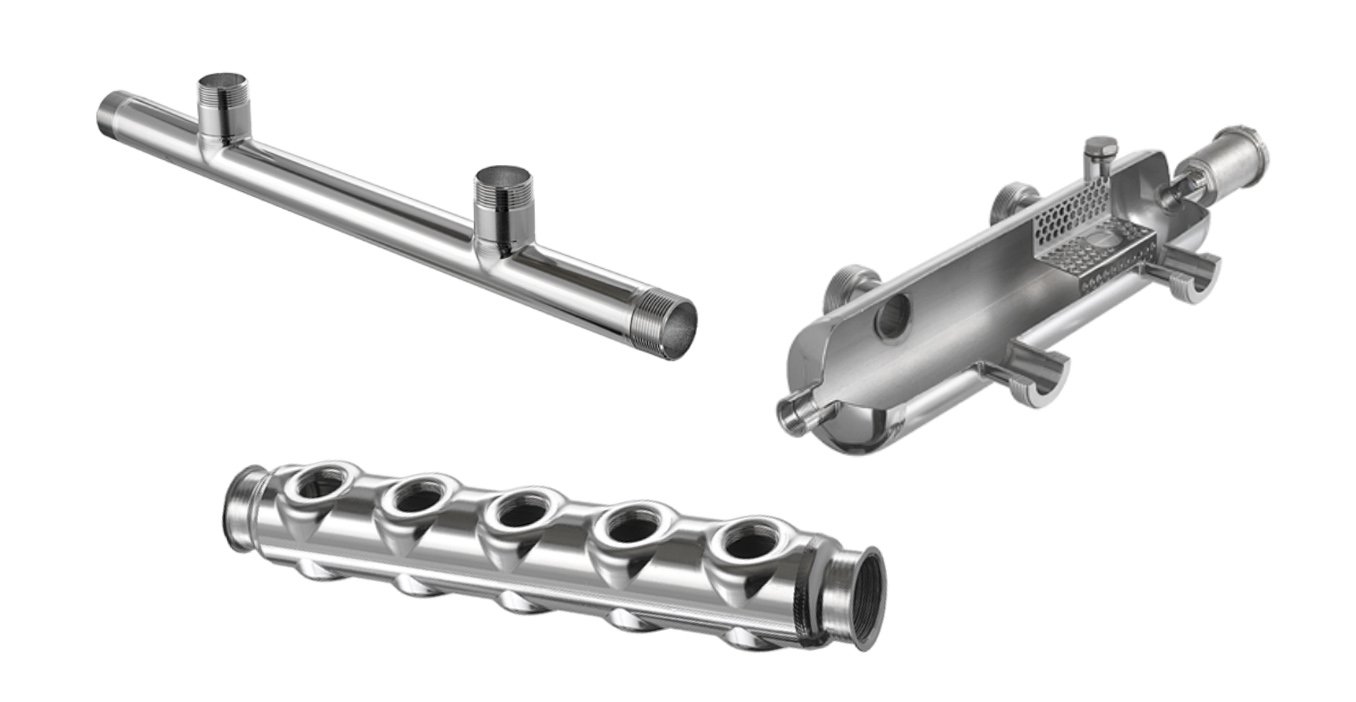
Materials: the resilience of AISI 304 steel.
When it comes to building manifolds for pressurization units and manifolds for heating systems, the choice of materials is crucial. AISI 304 stainless steel stands out as an excellent option because of its remarkable resistance to extreme environments. AISI 304 stainless steel, known for its corrosion resistance and high ductility, is a reliable solution for a variety of applications by offering increased resistance to corrosion and pitting in harsher and more aggressive environments. The durability and strength of this type of steel ensures that manifolds are able to withstand harsh conditions, including high temperatures, pressure differentials and chemical exposures.
Integration of collectors into heating systems.
Integrating collectors into heating systems is a strategic choice that brings numerous benefits:- they act as a central distribution hub, allowing efficient circulation of heating fluid throughout the system
- they connect multiple heating zones or circuits, enabling independent temperature control and regulation in different areas
- facilitate even heat distribution and ensure optimal comfort
- ensure better energy efficiency.
Integration of manifolds into pressurization units.
Pressurization units play a key role in maintaining the optimal pressure levels required by various industrial processes or large commercial or private buildings. Hydraulic manifolds therefore are essential components within these units, as they:- allow precise control and regulation of pressure by operators
- increase the reliability of the pressurization system by preventing damage caused by excessive pressure fluctuations
- ensure effective pressurization and depressurization cycles
- increase the safety of pressurization units by incorporating features such as safety valves and pressure sensors, which enable monitoring and control of system performance.